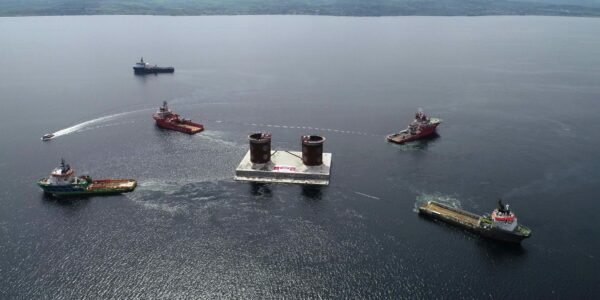
To solve technical issues and problems, highly specialized and innovative solutions have been developed in the past years.
Get in touchTo solve technical issues and problems, highly specialized and innovative solutions have been developed in the past years.
Get in touchA ballast system was designed and developed for the Çanakkale bridge project with one single goal; to run a flawless remote controlled ballasting operation. The challenge with ballasting large floating caissons with high accuracy and large flow capacities lies within the control of the flow, the system and the distribution.
This resulted in development of two 20ft ballasting manifolds, fitted with high-tech automated valves and pipework for distribution of 1200-1300m3 of water per hour. A single manifold was able to accurately distribute water to 15 clusters at one time and was fitted with a de-ballast pump of 1000m3/hr capacity in order to empty the clusters. It was even possible to re-distribute the water within the caisson. In total 120.000 m3 of seawater was pumped through the system.
Both the hardware as the software of this ballast system were specially designed. The entire system could be remote controlled by connecting to a RAYANT network system. By interconnecting the manifolds (pipework and data) a 100% redundant system was created.
Being container sized, transport and handling of the system could be done with standard lifting equipment and lorries.
Project 1915 Çanakkale Bridge ProjectThe Monaco government requested NFM and Strukton to perform dry maintenance on the 3m diameter hinge which connects the floating dike (batardeau) to the mainland structure (abutment). This resulted in development of a 15m deep and 10m wide habitat. The very limited space in which the habitat installation and hinge maintenance had to take place (ie. a 1m narrow joint) required this this special solution.
Making use of the principle of bicycle tires, a box-section steel U-shaped backbone was fitted with 4 inflatable rubber seals, 2 on front and 2 on back side. Deflated, the structure could fit inside the 1m joint. Once mounted and secured, the seals were partially inflated with water and topped of with air (3 bar maximum pressure), to create a double watertight seal against the floating dike and abutment.
Other special features: first an underwater vertical concrete patch had to be casted with high precision (<5mm) in order to create a smooth connecting surface for the seals. Structural design of the habitat was made for Hs=2.8m swell waves from sea, at which locking structures (cables and cylinders) could hold the habitat safely in position.
In total the habitat functioned for 3 months, in which period the maintenance of the hinge was completed.
Project Inflatable Barrier MonacoImmersion of tunnels is a methodology which relies on high accurate survey systems and control of movements / forces in order to place the tunnel elements within tight tolerances. In order to limit unsafe manual operations within the tunnel during the immersion operation, a remote controlled immersion system was first developed for the Busan Geoje (South Korea) project.
The basis was to centralize the critical operations from 1 command vessel (main immersion pontoon), from which the main systems could be remote operated. Systems controlled from the command vessel were;
A significant increase in the need for offshore wind-generated-energy makes for new technologies. Especially at offshore locations of 40-80m depth the use of so-called Gravity Based Foundations (GBF) is a growing market. Strukton Immersion Projects has developed a technology where installation of this type of structure can be executed without the use of floating cranes or lifting equipment.
The principle of this installation method is based upon a remote controlled ballasting system, which fills up the chambers inside the GBF in a controlled manner. This way the installation of this type of structure can be managed within 5-10cm vertical accuracy in winds up to 7 Bft and waves of Hs 1.5m.
Another important principle of this method is the use of a 3 or 4-point line and anchor system, where standard anchor handing tugs are deployed in line between the anchor and the GBF. This way also the horizontal plane position is controlled within 5-10cm of the target position (depending on the environment).
This system was successfully used in the installation of 5 – 6500t GBF structures off the coast of Blyth (UK) and installation of 2 – 60000t caissons in the Dardanelles Straight near Çanakkale (TUR).
Project Blyth Offshore Wind DemonstratorSuccessful immersion of tunnel elements relies on high-accurate positioning of the elements in relation to the theoretical alignment. In extreme conditions (large depths, high winds, currents, etc) this can be challenging, and could lead to a high amount of operational cancellations (downtime).
In order to overcome this an External Positioning System (EPS) was developed. This system was built up of two portal shaped “legs” which were connected to the roof of the element. Once the element was placed coarsely on the seabed (gravel), the hydraulically operated legs were activated and autonomous fine-positioning could be done.
This way secure and high-accurate positions within the set tolerances were reached, while operating within design winds/currents.
Project Busan Geoje Fixed LinkCan we assist you with a great project or are you interested in a position with us? Do not wait any longer and contact us directly!